|
Roughing and Pocketing...
A comprehensive
machining cycle.
ESPRIT’s comprehensive pocket
machining cycle handles straight wall pockets, tapered pockets, and
through or blind pockets. Whether they are simple squares or pockets with
complex irregular boundaries and a large number of multi-level islands and
bosses or sub-pockets, ESPRIT will drastically simplify your programming.
The ESPRIT Pocketing cycle provides full tool control and extensive
automation for roughing and finishing pockets in one simple step.
The Pocketing cycle supports
concentric outside-in and inside-out cutting with a constant overlap,
bi-directional zigzag, and one way zigzag movements. Finishing options
provide cutting tool and condition choices for finishing the walls and/or
the floors with the same or different tools, with individual stock
allowances and step over control for each cut.
|
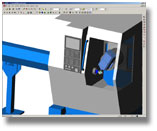 |
- Full tool control
- Extensive automation
for roughing
- All in one simple step
|
|
Contouring
...
Set the machining
parameters and let ESPRIT create the tool path.
You’ll find ESPRIT’s contour
machining cycle an important tool with universal applications for a wide
variety of machining tasks. This flexible cycle is ideal for profile
cutting, roughing, slotting, semi-finishing, and finishing straight or
tapered walls with constant or variable cutting depths. You simply set
the machining parameters and ESPRIT reads the various feature properties
to create tool path to cut any shape. When detailed tool control is
needed, you can rely on the Contouring cycle to manage the individual tool
movements, while allowing you to control the machining parameters at every
point during a cut.
|
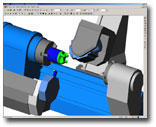 |
- ESPRIT reads feature
properties to create tool path to cut any shape
|
|
Rest Machining ...
Automatically performs
pocketing and contouring of uncut areas.
This intelligent cutting cycle
recognizes the machining operations and cutting tools associated with a
given feature of the part, and automatically compares the work piece “as
machined” to the original part “as designed”. Using this knowledge the
Rest Machining cycle automatically performs machining (Pocketing and
Contouring) of the uncut areas of remaining material. Use this cycle to
easily perform roughing and pre-finishing work with optimal cutting tool
choices.
|
|
- Automatically compares the work
piece "as machined" to original part "as designed".
|
|
Drilling and Hole Making
...
Up to 13 point to point
machining cycles are available..
Choose between ESPRIT’s
machining cycles, your machine tool’s canned cycles, or use a combination
of both. You have the freedom of choice. Drilling, peck drilling,
boring, taping and up to thirteen other point-to-point machining cycles
are available. Use one simple step in the Process Manager to cut complex
holes that require multiple cycles and several tools. As an example: spot
drill with chamfer, through drill, counter bore, and ream a set of holes,
all in one easy step. Machine internal or external right or left hand
threads using ESPRIT’s Thread Milling machining cycle. The Spiraling
cycle is well suited to milling and counterboring holes. In each case
ESPRIT will automatically generate optimized tool path minimizing the
cycle time.
|
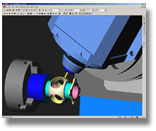 |
- Automatically generate optimized
tool path
- Minimize cycle time
|
|
Custom Machining Cycles
...
Control individual
cutting tool movements.
ESPRIT’s collection of Custom
machining cycles lets you control individual cutting tool movements. The
Insert technology function is available to adjust machining parameters
within a machining cycle at any point during the cut. Or use the Custom
cycle to insert commands, in-line G-code, and special cutting tool
movements at any point in the CNC program. Take advantage of the Park
instruction to pause the cutting process and retract the cutting tool for
part/tool inspection. Use the Tool Path Editor to edit the tool path as
if it were geometry to make special modifications to the tool path.
|
|
- Insert
- Park
- Tool Path Editor
|
|
FreeForm 3D Surface and
Solid Machining...
Cut complex 3D freeform
shapes.
SolidMill
FreeForm uses the ESPRIT solid machining engine to cut complex 3D
free-form shapes. Specifically designed to handle the most challenging
requirements of the mold, die, and tool making markets, ESPRIT provides
you with a powerful set of tools and a large selection of machining cycles
for roughing, semi-finishing, finishing, and re-machining.
|
|
FreeFrom Roughing ...
The FreeForm 3D Roughing cycle rough
machines any complex 3D shape from any shape stock. Similar to the
SolidMill Traditional Pocketing cycle, this 3D machining cycle performs
zigzag and offset style rough machining on even the most complex set of
3D solids/surfaces.
|
|
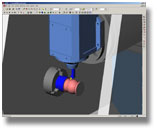 |
|
FreeForm Finishing
...
With the choice of seven different
semi-finishing and finishing cycles you can easily create all the tool
path necessary to machine your part. Use one cycle for your entire
part, or optimize your machining by defining containment boundaries.
Machine different zones of your part using the cycle and cutting style
most appropriate.
|
|
|
|
Z-Level Machining
...
Excellent for High Speed
Machining.
This cycle
identifies near vertical and near horizontal areas and allows the operator
to choose different cutting strategies for each area. Z-Level Machining
offers both roughing and finishing options using one or two tools in a
single cycle. It is an excellent cycle for High Speed Machining,
providing very smooth, continuous tool path.
|
|
Rest Material
Re-Machining ...
Automated Re-machining
of uncut areas.
Re-machining of uncut areas of your part
is automated through the Rest Material cycle. Select a cutter and ESPRIT
will automatically remove all possible remaining material using any one of
a number of cutting styles. Choose from pencil tracing, lace cutting,
parallel flowline, and spiral movements. This maximizes part quality and
minimizes bench work.
|
|
- Pencil tracing
- Lace cutting
- Parallel flowline
- Spiral movements
|
|
Remaining
Stock Machining ...
Use
Surface, Solid
and STL models for stock.
All of the FreeForm machining cycles are
optimized for machining from regular and irregular shaped stock/workpiece.
Surface, Solid and STL models may be used as stock, as well as the results
from previous machining operations. All cutting is optimized and
contained, or limited to the volume of material between the stock and the
final part, resulting in significantly reduced machining times and
extended tool life.
|
|
High Speed
Machining
Create smooth continuous tool movement.
Every ESPRIT
machining cycle includes a number of High Speed Machining options to
insure the creation of smooth, continuous movements while maintaining
constant loads on the cutting tools. Whether it’s HSM to cut hardened
materials, minimize cycle times, or both, ESPRIT supplies the tools to get
the results you need. Choose from sharp corner smoothing, loop style
bridge movements, ramp and helical entry into material, spiral style
cutting with constant overlaps, tangency entry, constant Z-Level cutting,
and many more. Included within the Universal Post Processor is HSM
optimization for NURBS and Spline curve G-code output.
|